Industrial Maintenance Management!!
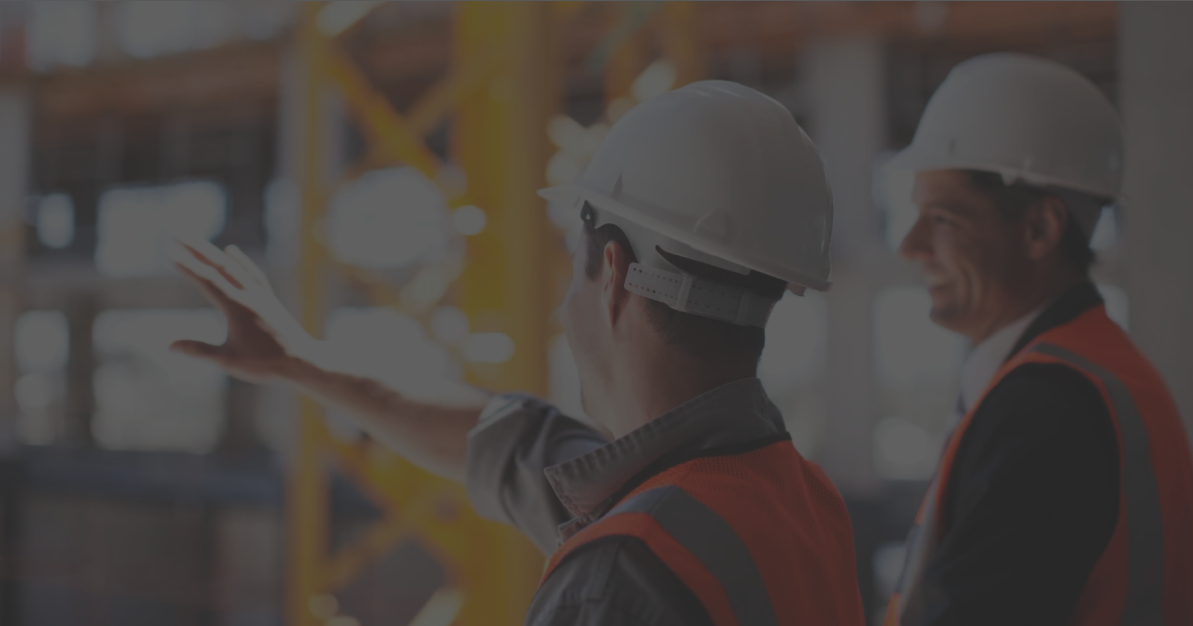
The management of industrial maintenance is an increasingly important process for the operation of companies, allowing to reduce costs, improve the efficiency of operations and extend the useful life of equipment.
In the current market, however, it is necessary that this process is accompanied by methodologies and tools that allow giving more precision and basis to the maintenance of machines and installations used in production.
This is the case of systems such as In Motion Facilities s , which assist in collecting data for maintenance activities, also maintaining the history of each equipment.
Next, learn more about the importance of industrial maintenance management and how In Motion Facilities can make this work more efficient.
Industrial Maintenance Management: why is it important?
Like other processes of optimization of managerial tasks, industrial maintenance management aims to reduce the costs involved in the company's operations . In this case, we refer to the possible losses due to the inadequate functioning of the equipment.
When a machine breaks down, it can lead to delays and other problems that impact the production cycle. Therefore, it is essential to calculate these costs to try to offset them.
In addition to the savings with this type of setback, industrial maintenance management also allows you to reduce maintenance teams and make their activities more efficient. The faster the service is performed, the less chance of losses.
Another important gain refers to the allocation of personnel, since there is a better planning of maintenance activities and also the frequency with which they must be carried out . This even favors the monitoring of technicians, in order to understand their routine and evaluate their performance.
When equipment maintenance is up to date, the safety of workers who deal directly with this machinery is increased. As the functioning of these components is monitored, it becomes easier to identify problems and trigger teams to carry out maintenance.
Along the same lines, machines that are frequently monitored and verified through preventive and predictive maintenance operate within the normal range, which helps to increase their useful life and reduce the costs of replacing equipment .
And by running smoothly, processes are guaranteed to run as expected, bringing more reliability to shop floor operations .
Finally, we cannot fail to mention the importance of industrial maintenance management to comply with regulations and legislation . An example is the minimum number of employees required to perform certain tasks.
Types of Industrial Maintenance
Within industrial maintenance management, there are three main types of activities:
Corrective maintenance
It consists of problem remediation activities, that is, it only happens when there is a stoppage in the equipment, either due to failure or clear indications that a breakdown may occur.
Preventive maintenance
Maintenance is carried out with the aim of reducing or avoiding failures and machine performance problems. Preventive activities involve inspections, renovations, component replacements, among others.
Another characteristic that marks this type of maintenance is the frequency according to the manufacturer's orientation. Based on this information, a periodic maintenance plan is drawn up to prevent early deterioration of the equipment.
In this sense, preventive maintenance also helps to monitor the wear of parts and predict a replacement plan.
predictive maintenance
This is the maintenance performed to verify the performance of the equipment through the analysis of data such as temperature, vibration, pressure, among other chemical and physical evaluations.
The data collected from these analyzes helps to predict the deterioration of machines, as well as possible failures and their consequences.
Industrial Maintenance Indicators
Within industrial maintenance management, there are some important indicators to monitor the performance of machines on the factory floor, here are some:
MTBF (Mean Time Between Failures)
The MTBF or Mean Time Between Failures indicates the total time when there is an average good health between repairable machine inaccuracies. This allows for reliability analysis of a machine.
Check out an example: a machine works for 12 hours in a day. In those 12 hours, she presents three problems in succession. In the first one, it took 5 minutes to repair; in the second, 10 min; in the third, 15 min. This triggered a total of 30 minutes of repair. Thus, we can calculate the MTBF:
MTBF = (TD – ΣTR) / QP
MTBF = (12*60 – 30) / 3 = 230 minutes
Where:
TD: Time Available
ΣTR: Sum of Repair Time
QT: Number of Stops
This value demonstrates that, during the entire 12-hour period, the factory must program itself and consider that, every 230 minutes, a failure will occur.
MTTR (Mean Time To Repair)
Average time to repair looks at the time employees have a machine up and running again. In short: it measures the team's ability to fix the flaw.
To perform the calculation, you need to divide the total time spent on repairs, also dividing by the total value of repairs made within the period. Let's use the information from the previous example:
MTTP = ΣTR / QP
MTTR = (5 + 10 + 15) / 3 = 10 minutes
Where,
ΣTR: Sum of Repair Time
QT: Number of Stops
The average time taken for repairs is 10 minutes. That is, the factory must schedule itself to have an average time of 10 minutes for repairing the machines. With these numbers, it becomes possible to identify downtime problems.
DTM - Technical Availability of Maintenance
It primarily means the availability of steady state, considering only equipment downtime due to stops for effective corrective maintenance. That is, the downtime due to other stops, such as preventive maintenance, logistics and supply delays, for example, is excluded from the calculation, as they are considered ideal, and only the downtime is evaluated, used for corrective maintenance action.
The calculation of the technical availability of maintenance is done using the mean time between failures divided by the sum of the mean time between failures and the mean time to repairs. Considering the same data as the previous example, it would look like this:
DTM = MTBF / (MTBF + MTTR)
DTM = 230 / 230 + 10
DTM 0.9583 or 95.83%
How the MES System facilitates the maintenance of equipment in the industry
The MES system allows monitoring the use of equipment, analyzing the time of use and the predefined limits to ensure that they do not exceed the maintenance requirements stipulated by the manufacturer.
The tool aggregates data that provides a complete view of problems and failures, including detailed historical information . Thus, it becomes easier to determine performance indicators that are reliable and true for each piece of equipment.
With more precise control over machinery data and maintenance activities, there is an improvement in the functioning of the equipment and an increase in its useful life . As we have seen, this is essential to reduce downtime risks and also for workers.
Byte In Motion develops customized systems for its clients, customizing them according to project priorities. InMotion Facilities is a factory floor management platform that manages the execution and operation of industrial manufacturing, from production scheduling to final product dispatch.
The tool generates information in real time through modules focused on production, scheduling, quality, maintenance and materials, in addition to allowing a comparison between what was planned and what is actually being executed. Discover InMotion Facilities and find out how we can help your company. Talk to our experts !